The machining of complex aluminum parts occupies an important position in the modern manufacturing industry. Aluminum alloy, as a lightweight and high-strength material, is widely used in aerospace, automobile manufacturing, electronic communications, medical equipment and other fields. With the continuous advancement of technology, the requirements for the machining of complex aluminum parts are getting higher and higher, requiring not only high precision and good surface quality, but also high machining efficiency and low cost. This article will introduce in detail the key technologies, process flow and common problems and solutions for the machining of complex aluminum parts.
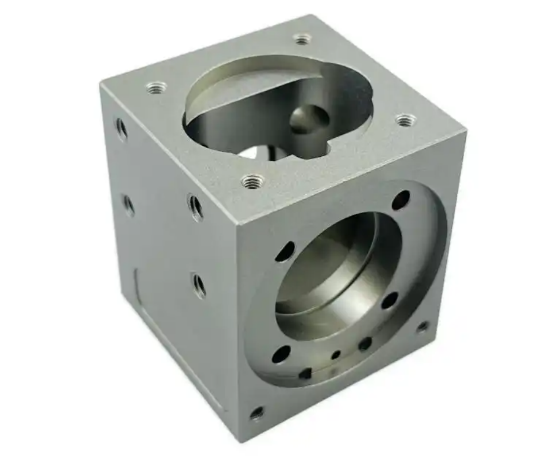
Key technologies for machining of complex aluminum parts
The key technologies for machining complex aluminum parts mainly include CNC machining technology, high-speed cutting technology, five-axis linkage machining technology and precision measurement technology.
1. CNC machining technology: CNC machining technology is the basis for high-precision machining of complex aluminum parts. Through programming, CNC machine tools can perform precise machining according to predetermined trajectories and parameters to ensure the dimensional accuracy and shape accuracy of parts. In the machining of complex aluminum parts, CNC machining technology can achieve multi-axis linkage to meet the machining needs of complex curved surfaces and special-shaped structures.
2. High-speed cutting technology: High-speed cutting technology is an important means to improve processing efficiency. By increasing the cutting speed and feed speed, the processing time can be significantly shortened, while reducing the cutting force and cutting heat, which is conducive to maintaining the processing accuracy and surface quality of parts. In aluminum processing, high-speed cutting technology can also reduce tool wear and extend tool life.
3. Five-axis linkage processing technology: Five-axis linkage processing technology is the key to achieving one-time forming of complex parts. Through the simultaneous movement of five axes, parts with complex curved surfaces and special-shaped structures can be processed without multiple clamping and changing workstations, which greatly improves processing efficiency and accuracy. In addition, five-axis linkage processing technology can also realize automatic tool replacement and compensation, further improving the level of automation of processing.
4. Precision measurement technology: Precision measurement technology is an important means to ensure the processing quality of complex aluminum parts. Through high-precision measuring equipment and measurement methods, the size, shape, position, etc. of parts during the processing process can be monitored and fed back in real time, and processing errors can be discovered and corrected in time to ensure the processing quality of parts.
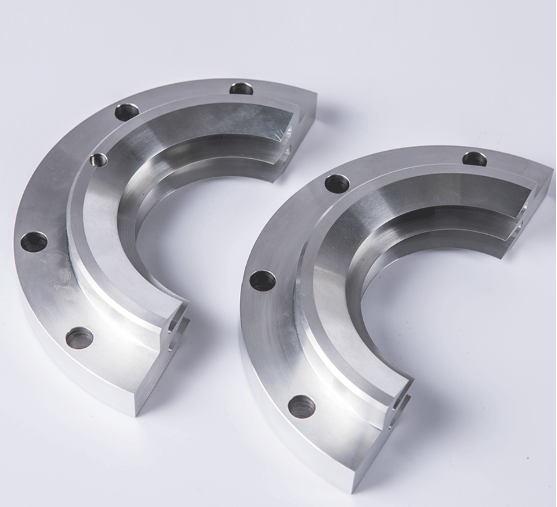
Process flow of aluminum processing of complex parts
The process flow of aluminum processing of complex parts mainly includes material preparation, blank manufacturing, rough machining, semi-finishing, finishing, inspection and acceptance.
1. Material preparation: Select suitable aluminum alloy materials according to the design requirements and processing requirements of the parts. At the same time, pre-treat the materials, such as deburring, cleaning, drying, etc., to ensure that the surface of the materials is clean and free of impurities.
2. Blank manufacturing: Select suitable blank manufacturing methods according to the shape and size of the parts, such as casting, forging, extrusion, etc. During the blank manufacturing process, it is necessary to ensure that the dimensional accuracy and shape accuracy of the blank meet the requirements of subsequent processing.
3. Rough machining: Rough machining is the process of removing excess material from the blank. By selecting appropriate cutting parameters and tools, the blank is rough-machined to make it close to the final shape and size. During the rough machining process, it is necessary to pay attention to the balance between cutting efficiency and tool wear to ensure processing efficiency and processing quality.
4. Semi-finishing: Semi-finishing is the process of further processing based on rough machining. By adjusting the cutting parameters and tools, the parts are semi-finished to further improve their dimensional accuracy and shape accuracy. During the semi-finishing process, it is necessary to pay attention to the balance between machining accuracy and surface quality to ensure that the machining quality of the parts meets the requirements of subsequent processing.
5. Finishing: Finishing is a key step to ensure the final dimensional accuracy and surface quality of the parts. By selecting appropriate cutting parameters and tools, the parts are finished to make their dimensional accuracy and shape accuracy meet the design requirements. At the same time, it is necessary to pay attention to the control of surface quality to ensure that the surface of the parts is smooth, without scratches, cracks and other defects.
6. Inspection and acceptance: Inspection and acceptance are important links to ensure the quality of part processing. Through high-precision measuring equipment and measurement methods, the size, shape, position, etc. of the parts are comprehensively inspected to ensure that the processing quality of the parts meets the design requirements. At the same time, the parts are visually inspected and functionally tested to ensure that the parts are defect-free and damage-free and can meet the use requirements.
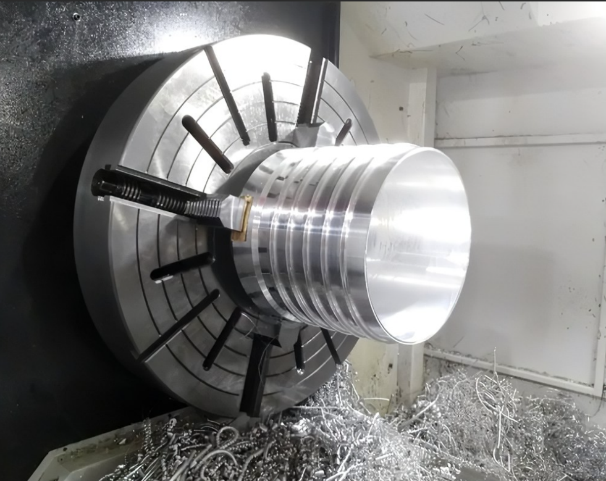
Common problems and solutions in the processing of complex aluminum parts
In the process of processing complex aluminum parts, some problems are often encountered, such as tool wear, processing deformation, poor surface quality, etc. In response to these problems, corresponding solutions need to be taken.
1. Tool wear: Tool wear is an important factor affecting processing efficiency and processing quality. In order to reduce tool wear, you can choose suitable tool materials and tool structures, such as carbide tools, coated tools, etc. At the same time, optimize cutting parameters, such as cutting speed, feed speed, cutting depth, etc., reduce cutting force and cutting heat, and reduce tool wear. In addition, regularly check and replace the tool to ensure that the tool is in good condition.
2. Processing deformation: Processing deformation is an important factor affecting the processing accuracy of parts. In order to reduce processing deformation, the following measures can be taken: First, optimize the blank manufacturing process, such as using reasonable casting, forging, extrusion and other processes to improve the strength and rigidity of the blank; second, optimize the processing technology, such as using step-by-step processing, symmetrical processing and other methods to reduce stress concentration and deformation during processing; third, use appropriate clamping methods and clamping forces to avoid deformation of parts due to excessive clamping force during processing.
3. Poor surface quality: Poor surface quality is an important factor affecting the performance and aesthetics of parts. In order to improve the surface quality, the following measures can be taken: First, choose appropriate cutting parameters and tools, such as high-speed cutting technology and fine cutting.
Post time: Mar-06-2025