More molybdenum is consumed annually than any other refractory metal. Molybdenum ingots, produced by melting of P/M electrodes, are extruded, rolled into sheet and rod, and subsequently drawn to other mill product shapes, such as wire and tubing. These materials can then be stamped into simple shapes. Molybdenum is also machined with ordinary tools and can be gas tungsten arc and electron beam welded, or brazed. Molybdenum has outstanding electrical and heat-conducting capabilities and relatively high tensile strength. Thermal conductivity is approximately 50% higher than that of steel, iron or nickel alloys. It consequently finds wide usage as heatsinks. Its electrical conductivity is the highest of all refractory metals, about one third that of copper, but higher than nickel, platinum, or mercury. The coefficient of thermal expansion of molybdenum plots almost linearly with temperature over a wide range. This characteristic, in combination will raise heat-conducting capabilities, accounts for its use in bimetal thermocouples. Methods of doping molybdenum powder with potassium aluminosilicate to obtain a non-sag microstructure comparable to that of tungsten also have been developed.
The major use for molybdenum is as an alloying agent for alloy and tool steels, stainless steels, and nickel-base or cobalt-base super-alloys to increase hot strength, toughness and corrosion resistance. In the electrical and electronic industries, molybdenum is used in cathodes, cathode supports for radar devices, current leads for thorium cathodes, magnetron end hats, and mandrels for winding tungsten filaments. Molybdenum is important in the missile industry, where it is used for high-temperature structural parts, such as nozzles, leading edges of control surfaces, support vanes, struts, reentry cones, heal-radiation shields, heat sinks, turbine wheels, and pumps. Molybdenum has also been useful in the nuclear, chemical, glass, and metallizing industries. Service temperatures, for molybdenum alloys in structural applications arc, is limited to a maximum of about 1650°C (3000°F). Pure molybdenum has good resistance to hydrochloric acid and is used for acid service in chemical process industries.
Molybdenum Alloy TZM
The molybdenum alloy of greatest technological importance is the high-strength, high-temperature alloy TZM. The material is manufactured either by P/M or arc-cast processes.
TZM has a higher recrystallization temperature and higher strength and hardness at room and at elevated temperatures than unalloyed molybdenum. It also exhibits adequate ductility. Its superior mechanical properties arc due to the dispersion of complex carbides in the molybdenum matrix. TZM is well suited to hot work applications because of its combination of high hot hardness, high thermal conductivity, and low thermal expansion to hot work steels.
Major Uses Include
Die inserts for casting aluminum, magnesium, zinc, and iron.
Rocket nozzles.
Die bodies and punches for hot stamping.
Tools for metalworking (due to the high abrasion and chatter resistance of TZM).
Heat shields for furnaces, structural parts, and heating elements.
In an attempt to improve the high-temperature strength of P/M TZM alloys, alloys have been developed in which titanium and zirconium carbide is replaced by hafnium carbide. Alloys of molybdenum and rhenium are more ductile than pure molybdenum. An alloy with 35% Re can be rolled at room temperature to more than 95% reduction in thickness before cracking. For economic reasons, molybdenum-rhenium alloys are not widely used commercially. Alloys of molybdenum with 5 and 41% Re are used for thermocouple wires.
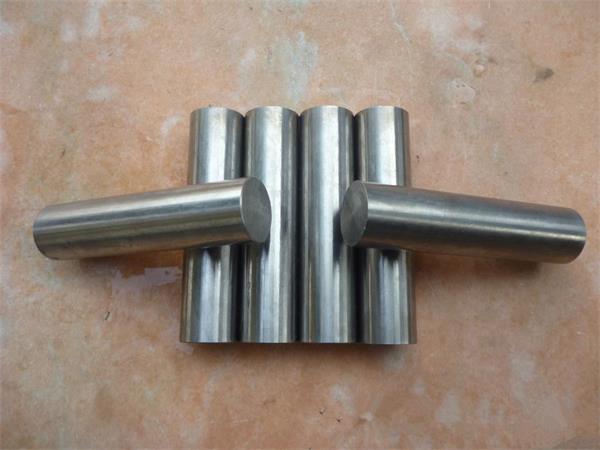
Post time: Jun-03-2019